Increasing Distillate Production at Least Capital Cost
Investing in improvements to the atmospheric crude unit can deliver increased distillate yields with short payback times
JOE MUSUMECI, STEVEN W STUPIN, BRANDON OLSON AND CARLOS WENDLER
Ascent Engineering
This is the second of two articles which discuss changes to the crude unit to increase distillate production from each barrel of crude processed. The first article reviewed operational adjustments that require zero capital investment. This second article focuses on atmospheric crude unit improvements that require minimal as well as major capital investment with short payback to further increase distillate yield. Improvements to the vacuum unit, which are not discussed here and will be covered in a future article, can also offer tremendous gains to the refiner’s distillate production.
Historically, most US refineries have been designed and operated to maximise gasoline production as a response to the needs of transportation that have led the consumer market. However, shifts in worldwide fuel consumption patterns have caused a decrease in the demand for gasoline and an increase in the demand for diesel fuel. This trend, discussed in our first article (PTQ Revamps 2014), has led to a current diesel price differential of about $0.23/gal over gasoline and is expected to increase to over $0.70/gal by 2030 if the trends continue. Contributing factors to this changing consumption pattern include increased demand in developing countries, a focus on reducing greenhouse gas emissions that has led to more stringent automotive fuel efficiency standards, and increased blending of renewable fuels. Adjusting to these market conditions can allow refiners to maximise refinery profitability by producing higher yields of the most valuable distillate products.
Opportunities for increasing distillate yield range from operational tweaks that require no capital, as discussed in the first article, to simple modifications that can be potentially implemented without a unit shutdown, to major capital projects. Operational tweaks can be identified by test run most successfully with the help of process simulation, but are often limited by the capabilities of the existing equipment. A refiner who is willing to invest in capital projects may benefit the most from a well thought out design plan which will yield the greatest return on investment and maximum profitability.
A key to implementing any plant design plan is to have accurate simulation and design. A simulation tuned to actual plant data is often useful to benchmark the current operation and can be used to compare alternative concepts for optimisation of the proposed upgrades. The alternative cases should focus on variables which have the greatest impact on distillate yield with effort to minimise capital cost often by maximising the reuse of existing equipment. Refinery and unit product specifications should be reviewed to ensure they are current and their purpose understood. This process may require challenging some of the unit’s current target specifications by identifying unwarranted limits on unit operations and possibly resulting in unnecessary overprocessing and increased operating costs. With these specific areas in mind, concepts can be assessed to narrow down options to those with the greatest financial incentives. Simulation and design experience, such as that provided by a skilled process design firm, is critical if the refiner wants to identify new ideas and the best projects to maximise profitability.
Atmospheric tower modifications to increase distillate production
Maximising the capability of the atmospheric tower is often the primary focus when considering crude unit modifications. Improving atmospheric tower operation usually requires the least amount of capital for a given increase in diesel yield. The following sections focus on atmospheric tower modifications that go beyond simple operational adjustments and will require some capital investment in order to improve distillate recovery.
Stripping steam in the atmospheric tower and side strippers
Increased stripping steam vaporises additional distillate range material from the crude; this requires adequate tower capacity and heat removal capabilities to condense and recover the additional distillate above the flash zone. The first article of this series included a case study demonstrating how, in one refinery, increasing the stripping steam rate (and the tower operating pressure, to offset the increase in percent of flood) significantly increased diesel yield and refinery profits. Other refineries may have similar equipment or hydraulic constraints which limit the ability to increase stripping steam rates as a means to improve distillate product recovery. The extent of the equipment constraints could range from flooding in one or more tower sections or in a side stripper to limited condensing capacity or water dew point limitations in the overhead system. Specific modifications are required in order to tackle specific atmospheric tower system limitations which may exist when trying to maximise stripping steam.
Even though stripping steam rates represent a small portion of the tower’s vapour loadings, flooding in one or more atmospheric tower sections or in a side stripper can be the first limit encountered when increasing stripping steam flow. In this case, a designer may consider installing higher capacity trays or replacing trays with packing. Increasing tray spacing is another option for greater debottlenecking. However, the reduction in theoretical stages that can result from this type of modification should be evaluated to ensure that the fractionation remains acceptable.
A thorough review of all auxiliary equipment is necessary to ensure that the limits of the other equipment have not been exceeded. If increased tray spacing or high capacity trays are insufficient to relieve the tower flooding, more extensive modifications may be required. The tower or side stripper diameter may need to be replaced with a new, larger tower section. The additional capacity that results from these modifications will enable the refiner to take advantage of increased stripping stream rates and subsequent increased distillate recovery.
Another common obstacle that can prevent or limit an increase in stripping steam rate is the inability to remove additional energy from the atmospheric tower. Heat removal can be limited by insufficient capacity in the overhead condensing system and increased pumparound duty. Options for increasing overhead condensing capacity include adding exchanger surface area with new exchanger bundles, reconfiguring the existing exchanger train, and adding a new exchanger or air cooler. A designer can evaluate whether heat is currently being rejected to water or air that can instead be recovered into the crude preheat train. Modifications to the tower pumparound circuit(s) should also be considered. Modifications can include changes to the pumps, piping, control systems, and exchangers with a review of the tower’s pumparound section trays or packing. Lower cost options include new impellers, piping jump overs, and exchanger bundles. Larger investment might include new heat exchangers and air coolers along with a major reconfiguration of the crude preheat train.
An accurate simulation model is paramount for the optimisation of the complex interactions between the tower pumparounds and the preheat train in order to maximise energy recovery and to minimise fractionation losses. If an accurate plant-matched simulation model does not already exist for the full crude unit, consider commissioning an experienced engineering firm to assist in developing this powerful and valuable tool.
Reduce atmospheric tower operating pressure
Like stripping steam, reducing the operating pressure of the atmospheric tower increases distillate recovery by reducing hydrocarbon partial pressure and increasing vapour rate, thereby allowing lighter range material to remain in the vapour phase at a given feed temperature. This helps to ‘lift’ heavier materials like distillate up the tower to increase recovery, but will increase vapour loadings because of the additional volumetric flow at lower density and therefore more volume which must be evaluated.
Lowering the pressure also has similar constraints to tower capacity and heat removal as in the previous stripping steam discussion. Lower pressures result in lower condensing temperatures, which lower the temperature driving force for heat transfer in pumparounds and the overhead condenser. Having an accurate simulation of the system will help identify and quantify effects such as this. Aside from cooling capacity, hydraulic limitations can also bottleneck a tower overhead system. The lower cost solution for fixing hydraulic problems can include installing low pressure drop valves, new exchanger bundles, and adding a parallel piping line. Larger investments might include new exchanger systems, and new nozzles and piping. Often, the source of the overhead capacity limit can also be the tower off-gas compressor which should be evaluated.
Improve atmospheric tower fractionation
Equipment modifications to improve fractionation typically focus on the effective operation of tower internals and may include installation of high efficiency or high capacity trays or packing. Generally, all atmospheric tower sections should be reviewed with improved fractionation as a goal to increase distillate recovery. Also, the designer should keep in mind that certain tower sections may require or benefit from additional design consideration to help maximise run length or maintain operational efficiency, for instance anti-fouling features for trays or packing in the wash and stripping sections, particularly with certain crude types known to have fouling effects.
Packing should also be considered to replace trays where the advantage of low pressure drop can be beneficial. In low pressure systems, the advantage of lower pressure packing can be that the same amount of stripping occurs with lower stripping steam rates. When revamping from trays to high capacity packing, separation efficiency needs also to be evaluated. A loss in separation efficiency is sometimes unavoidable if high capacity packing with lower surface area is considered. Lower surface area packing has higher capacity and is more fouling resistant, but has lower separation efficiency.
While new or modified tower internals may be sufficient to achieve the desired fractionation improvement, more extensive modifications may be required if these options do not achieve the desired fractionation. For example, the addition of a stripper on an AGO side draw that does not currently have one can be a lucrative option to recover incremental distillate. Additional fractionation improvements may warrant more costly options including adding additional tower height to increase the number of distillation stages or installing a new larger tower section.
Often fractionation and tray or packing performance deteriorates, and may go unnoticed for some time. In one medium-sized US refinery, the authors worked with engineering staff to evaluate and specify new trays in the atmospheric tower to increase distillate yield by a predicted 3.1 LV% of crude. The refiner had been having problems reliably drawing a consistent volume and quality of www.eptq.com AGO product, and product fractionation was poor. This condition continued for more than a year. A subsequent gamma scan of the atmospheric tower suggested some level of suspected damage to the wash and stripping section trays.
Figure 1 shows the atmospheric tower configuration, with the suspected damage noted. The poor fractionation in the wash and stripping sections had severely limited the ability to recover distillate from the crude feed, resulting in losses via the atmospheric tower bottoms. Diesel range material that was lost to the vacuum tower tied up vacuum unit capacity and was recovered as LVGO, which was cracked to lower value products in the downstream hydrocracker unit. Additionally, the excess diesel in the vacuum tower feed resulted in worsened vacuum system performance. This increased the tower pressure which resulted in an undesirable increase in residue product yield.

The authors developed a simulation model of the crude unit to help identify issues and predict the expected distillate yield. Simulation of the unit to match the plant data confirmed the suspected tray damage and quantified for the refiner the amount of unrecovered distillate. By installing new trays designed for updated process loadings, diesel recovery was significantly improved. Poorly designed but otherwise intact internals can have a similar effect and symptoms as the situation described here. In either case, a refiner may often operate the equipment with little suspicion that the condition could be resulting in a huge economic penalty.
In addition to replacing the trays, the authors recommended that the refiner make other adjustments including increasing the heater outlet temperature and stripping steam rates to further increase diesel yield. Table 1 shows the results of simulated cases for the plant match simulation, including predicted operation with the new trays and subsequent operational cases which increase the heater outlet temperature and tower stripping steam rate.
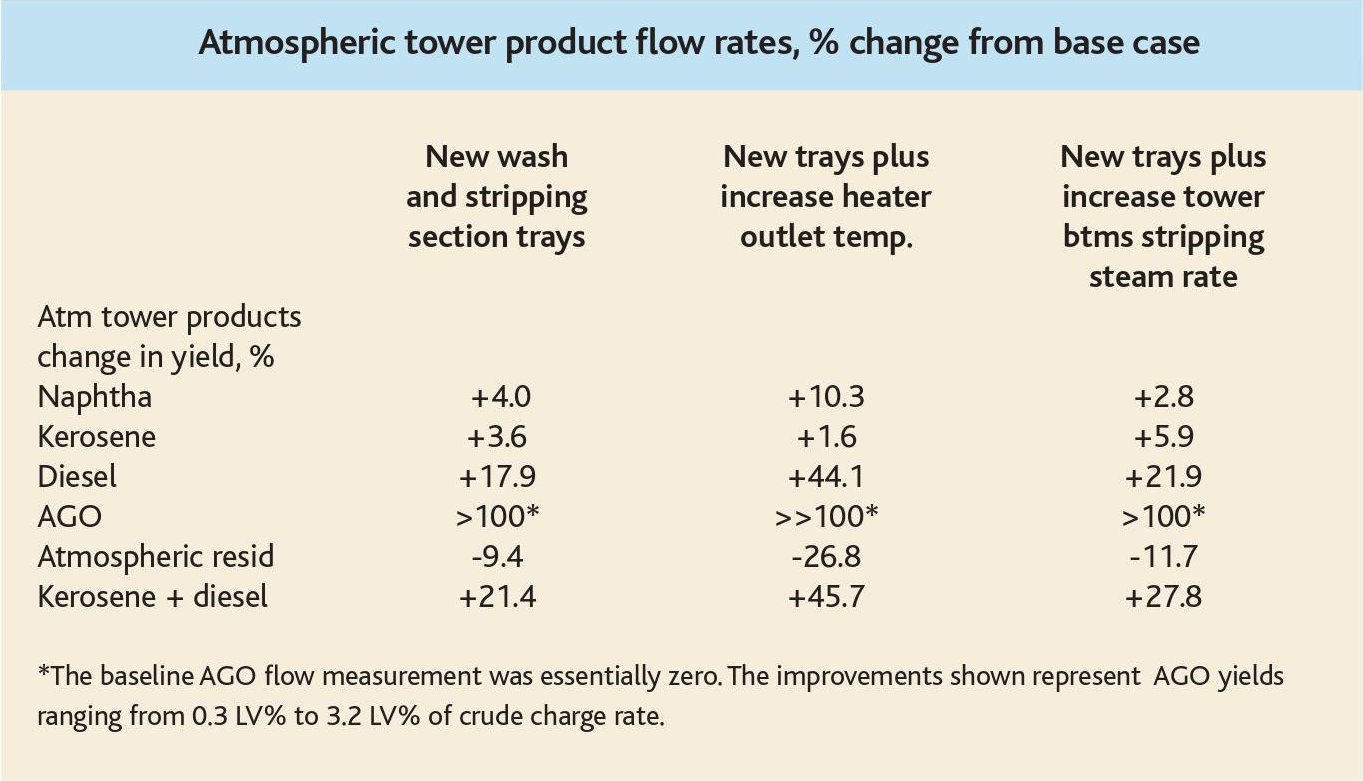
At this refinery, replacement of the atmospheric tower trays resulted in a predicted increase in kerosene and diesel yield by a total of 3.1 LV% of crude. Additional profits from this minor cost improvement are roughly $8.3 MM/year, based on this refiner’s estimated diesel recovery incentive of $30/bbl.
An additional benefit to replacing the trays was the reduction of the vacuum tower off-gas by a factor of 2.3, which significantly unloaded the refiner’s vacuum tower jets and improved vacuum, which allowed for increased gas oil recovery. The new atmospheric tower trays reduced the amount of lighter range material being sent to the vacuum tower, which relieved choking of the vacuum transfer line and helped debottleneck the vacuum system.
Atmospheric tower wash oil modifications
Some loss of distillate and AGO range material to the atmospheric tower bottoms is inevitable, even in already optimised equipment configurations. This can be due to excessive AGO wash oil rate exiting the bottom of the tower as overflash product. The primary function of the wash oil section is to reduce entrainment and black bodies in the vapour travelling upward from the flash zone. However, simply reducing the wash rate to minimise distillate and AGO losses from the atmospheric tower can come with severe consequences. Too low a wash rate can lead to dry wash zone internals. This results in fouling due to coke formation and also impacts distillate product quality due to entrainment of residue from the flash zone. There are a few modifications that a designer may consider in order to optimise the wash oil rate so as to minimise the loss of distillate material from the atmospheric tower.
One low cost modification for the wash section is to consider routing some LVGO from the vacuum tower to supplement the atmospheric tower wash oil. This option could be implemented without a shutdown by hot tapping an LVGO tie-in to the existing atmospheric tower wash oil supply line. Further modifications require a unit shutdown to improve the efficiency of the tower wash section internals.
Another modification that can be considered for the wash oil section is to replace the trays with a packed bed. Since wash trays require relatively high wash rates to de-entrain the vapours moving up the atmospheric tower from the flash zone, this option is best suited to atmospheric towers suffering from high overflash and subsequent loss of distillate to AGO range material. A packed bed allows for lower wash oil rates compared to trays, which in turn can minimise the loss of distillate and gas oil material in the overflash. For an existing tower, structured packing can increase the number of theoretical stages and improve fractionation, which can be advantageous if space is a concern. A packed bed of reduced diameter (in an internal cylinder) can further reduce wash oil requirements. The preferred combination for the wash bed is a combination of structured packing over grid. Any carefully vetted modification made to the wash oil section that results in reduced wash oil rate helps to minimise losses of distillate range material from the bottom of the atmospheric tower, which is critical for crude units that do not have distillate recovery in the vacuum tower section.
Atmospheric tower pumparound modifications
Evaluation of a tower’s pumparound section requires thorough review of the crude unit as a whole, due to the complex interaction between the atmospheric tower and the preheat train exchangers and, in some cases, pumparound exchangers that are used as heat or reboiler sources for other towers. Generally, increased pumparound duty results in increased energy imparted to the cold crude charge, which increases heater inlet temperature. For heaters that were previously at their limit, the outlet temperature can then be raised to increase lift in the tower which can be used to recover more distillate. The effect of increased pumparound rates within the tower is that internal reflux will increase below the pumparound, which helps sharpen fractionation in this section, but decreases fractionation above the pumparound where reflux decreases due to the extra heat removal below. The first article of this series discussed the benefits of optimising atmospheric tower pumparound rates and included a case study demonstrating how, in one refinery, even small operational adjustments to the AGO and diesel pumparounds improved diesel yield and refinery profits.
Some refineries may have one or more equipment constraints which limit their ability to adjust tower pumparound rates. Equipment limitations can range from flooding (tower capacity), insufficient heat removal (heat exchanger performance), and/or flow limitations (pump capacity). Lower cost pumparound modifications may include equipment rerate at higher design conditions, heat exchanger retube, or a new pump impeller. More extensive modifications may also include pump or heat exchanger replacement, or modifications to the tower internals in the pumparound section. It is important to review the changes and how they impact the rest of the crude unit, keeping in mind that the modifications should help the refiner achieve the end goal of increased distillate yield or capacity without sacrificing performance within the unit as a whole.
Atmospheric tower overhead system modifications
The atmospheric tower overhead system plays an important role in distillate yield. Minor changes to reflux rate or temperature can affect fractionation and subsequent distribution of the side cuts. The ability to maximise distillate production by means of increasing the reflux rate and lowering the overhead temperature to shift naphtha end range material into light distillates is typically limited by overhead condensing and pump capacity. Furthermore, care must be taken to avoid operating below the water dew point, which can increase localised corrosion and fouling in the overhead exchangers and on top tower trays due to acids and salts which concentrate in the first drops of water.
Lower cost upgrades to the overhead system may include rerated equipment, a bundle retube, or a new pump impeller or motor. More substantial capacity improvements may include replacement of exchangers, addition of air coolers, adding reflux or distillate pump services into independent operation, or installation of additional or larger reflux/distillate pumps. With sufficient condensing capacity available to reduce the reflux temperature, and with considerations made to avoid tower overhead system corrosion, a refiner can capitalise on increased distillate yield.
Any review that aims to minimise corrosion issues in the overhead system should begin at the desalter, where salts that are not removed end up in the tower’s overhead system. Common issues associated with the desalter include plugging of instruments, improper control of desalting chemicals, poor desalter water quality, malfunctioning desalter electrical grids, and insufficient wash water flow. Typical modifications are aimed at the target problem. Similar care must be taken to review the wash water system’s filters, water quality, and controls. It is also recommended to check wash water flow rates to ensure that sufficient free water remains after injection to prevent salt concentration, corrosion, and plugging in equipment. With a properly functioning desalter and wash water system as well as sufficient capacity in the overhead system, the refiner can make adjustments to the overhead’s cutpoint in order to achieve increased distillate yield.
Atmospheric heater and preheat train modifications
For many refiners, the limiting piece of equipment in the preheat train is the atmospheric heater. Heaters are often run at or beyond their design limits, and any way that a refiner can unburden this key piece of equipment will significantly impact crude unit operations. The goal is to maximise the heating duty that is provided by the other equipment in the preheat train so that an increased heater inlet temperature with the same heater outlet temperature (lower furnace duty) or increased heater outlet temperature (constant furnace duty) can be realised. Optimising the balance of heat duty provided by the preheat train and by the atmospheric heater is often limited by preheat train capacity, atmospheric transfer line or tower inlet device capacity, atmospheric tower pumparound exchangers or overhead condensers, or fuel quality at the heater itself.
Potential preheat train modifications include many of the topics previously discussed, such as exchanger modifications (adding or relocating surface area, changing the order of heat sources, or balancing flows), pump modifications (new impeller or motor), or new, larger piping or equipment altogether. Some consideration must be made when assessing the preheat train as an integrated system. For example, adding a parallel heat exchanger reduces velocities in adjacent exchangers, which accelerates fouling, thereby reducing overall heat transfer and heat exchanger performance. The performance of preheat train heat exchangers may also be reduced when operating exchangers designed for two-phase flow below their vaporisation design basis, as lower fluid velocities result in reduced heat transfer coefficients. An improved crude preheat design can be achieved with simulation and a thorough understanding of the temperatures and duties of the process streams available for crude preheat. In some cases, a pinch study of the crude preheat train may be justified.
In addition to preheat train modifications, there are changes that can be made to the heater itself. Low cost options may include a review of the burner management system, fuel gas system, and other heater controls to ensure optimum operation, or burner elements may need to be replaced. A larger investment might include retubing the heater for increased capacity and surface area, but this would be subject to the heater’s permit limitations. Then, having unburdened the heater with preheat train or heater modifications, the refiner gains flexibility for future operations. The refiner may choose to increase heater firing to raise the atmospheric tower flash zone temperature and lift more diesel. Alternatively, the refiner may choose to increase the crude charge while maintaining the same heater outlet temperature. It is important that the designer considers the preheat train modifications and the heater modifications together, while also considering future operational plans, in order to optimise the whole system for increased distillate yield.
Atmospheric preflash tower
A preflash tower is used to remove lighter material from the crude before it reaches the atmospheric tower. The overhead product and side draw streams may be bypassed around the atmospheric heater and tower and routed to downstream units for further processing. This configuration allows the refiner to unload the atmospheric heater and tower, which can increase distillate recovery. A preflash tower can suffer from some of the same capacity or heat removal issues that the atmospheric tower often sees, so the debottlenecking tactics are similar and include strategies such as stripping steam and operating pressure optimisation, retraying the tower with increased tray spacing or with high capacity trays, or expansion of overhead condensing capacity. More significant modifications include replacing an existing preflash tower with a larger tower, or installing a new preflash tower and auxiliary equipment if the system does not already exist.
If the crude unit does not currently include a preflash tower, the addition of such a tower could help to substantially increase distillate yields. A preflash drum is also an excellent option to consider for a refiner who desires a preflash system to debottleneck the crude unit but does not wish to immediately invest the capital required to install an entire tower and its auxiliary equipment. The drum serves as single stage flash, the vapour from which must be routed to the atmospheric tower for further fractionation. The flashed crude exits the bottom of the preflash drum and is routed to the atmospheric heater. The refiner has the option to convert the system to a preflash tower in the future, which would include the auxiliary equipment and may allow the overhead vapour and/or a side draw stream to bypass the atmospheric tower altogether and be routed directly to downstream processing units.
In one US refinery, the authors designed a new atmospheric preflash tower as part of a crude unit revamp which increases middle distillate production by 25%. This crude unit expansion project is driven by new crude opportunities which have more naphtha and middle distillates than current crude slates. The refinery’s desire to process lighter crude necessitates capacity improvements in the areas being overloaded by the new crude, which ultimately will allow for an increase in overall crude unit capacity. Thus, the recommended modifications will bring flexibility to refinery operations and allow for increased distillate production either by processing inherently lighter crude slates (such as tight oils) or by increasing the regular crude charge by roughly 30% compared to current operation.
In order to handle the lighter crude and increased throughput, this debottlenecking project includes a number of modifications requiring significant capital investment, including new exchangers in the preheat train, and a new preflash tower with overhead system. A simulation modelling the new crude slate showed severe flooding in multiple sections of the atmospheric tower and limited heat removal capacity.
The preflash tower affords increased separation capability for the crude unit and was less costly than installing a new larger atmospheric tower with more overhead condensing and pumparound capacity. Additionally, stripping steam was added to the new preflash tower which recovers some of the lighter material that would otherwise be sent to the atmospheric tower. This saves adding additional condensing and pumparound capacity to the atmospheric tower. The preflash tower will be installed at the end of the hot crude preheat train before the atmospheric heater.
Modifications to the existing atmospheric tower include increased capacity of the diesel packed bed. The structured packing in the diesel pumparound bed will be replaced with a higher capacity type to avoid flooding in this tower section. One lower cost modification, a new kerosene pumparound draw and exchanger, was evaluated and also incorporated into the revamp project. The modelling work for this modification showed that the new pumparound vs crude exchanger could reduce the charge heater duty by 13%.
At this refinery, the 25% increase in middle distillate products (kerosene and diesel) amounted to significantly increased profitability with a very short payback period.
Conclusion
The demand for diesel continues to rise, as does its price incentive over gasoline, and refiners are wise to consider making capital investments to increase distillate yield. The decision for which capital modifications to pursue depend on many factors unique to each refinery and include examination of available crude slates, product strategy, unit configuration, and equipment capabilities, though economics ultimately govern the decision. Once a refiner has exhausted zero capital opportunities by optimising existing crude unit capability, attention should be turned to capital projects that provide great opportunity for a large return on investment.
A simulation matched and tuned to plant operation is key for determining where the atmospheric tower is limited and for exploring the refiner’s options for upgrades. All areas of the atmospheric tower and its auxiliary equipment should be analysed thoroughly, including stripping steam rates, tower flooding, heat removal capabilities, operating pressures and temperatures, wash oil, pumparounds, overhead system, and the preheat train including the atmospheric heater and preflash tower. Modifications to these subsystems can range from relatively inexpensive, such as replacing a pump impeller, to moderately priced, such as new tower internals or an additional exchanger shell, to major capital expenditure, such as major new equipment. Several examples were presented, showing how profitability was improved at several refineries. The authors have analysed atmospheric tower systems at numerous refineries and recommended modifications which have resulted in millions of dollars per year of increased profits. Modifications to the vacuum tower, which require a future article to fully address, represent another piece to maximising the refiner’s distillate yields. The current and future distillate premiums over gasoline present other significant unit configuration changes as compared to the historic crude and vacuum design intended to maximise gasoline instead of distillate yield. With the increased industry focus on distillate production, a refiner has a number of options across a range of price points to help him increase diesel recovery and maximise product profitability.
References
- Musumeci J, Stupin S, Schlosser S, Scholten T, Increasing distillate production at zero capital cost, PTQ Revamps, 2014.
- Annual Energy Outlook, Energy Information Administration, 2014.
- Kraus, R S, Stellman J M, Petroleum Refining Processes, International Labor Organization Encyclopedia of Occupational Health and Safety, 78, 2011.
- Sloley A W, Increase diesel recovery, Hydrocarbon Processing, Jun 2008, 85, 102.
- Golden S, Crude unit preflash drums and columns.
- Barletta T, White S, Crude overhead system design considerations, PTQ, Q3 2007.
- Sandu C, Wright B, Innovative solutions for processing shale oils, Hydrocarbon Processing, Jul 2013.
The Authors
Joseph (Joe) Musumeci is the founder of Ascent Engineering, Inc. (Houston, TX). Since 1997, he has been responsible for Ascent’s consulting and process design projects. He holds a BS in chemical engineering from Texas A&M University, and is a registered Professional Engineer in the state of Texas.
Steven W Stupin is a Technical Consultant and Senior Lead Process Engineer with Ascent Engineering, Inc. He has 26 years of refinery troubleshooting, revamp and design experience, and holds a BS in chemical engineering from the University of California Santa Barbara, and is a registered Professional Engineer in the state of California.
Brandon Olson is a Process Engineer at Ascent Engineering, Inc. He has 12 years of process engineering experience and holds a BS in chemical engineering from the University of California at San Diego. He is a registered professional engineer in the state of California.
Carlos Wendler is a Senior Lead Process Engineer with Ascent Engineering, Inc. He has 14 years of technical support, process design and operations experience covering a wide range of process units. He holds a BS in chemical engineering from New Mexico State University.